Les différences entre Kanban et Kanban d’emplacement
1. Kanban
Le kanban est une méthode de gestion de production. Créée en 1950 par Taiichi Ono, ingénieur pour Toyota, c’est une approche visuelle construite sur un système d’étiquettes (Kanban en japonais) afin de gérer du stock au niveau local à poste. Un système Kanban se traduit par une boucle située entre un client et son fournisseur à l’intérieur de laquelle un certain nombre d’étiquettes ou cartes vont circuler.
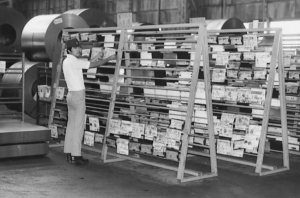
Premier tableau kanban, source : toyota-global.com
Un kanban est toujours associé directement à un produit. Il est systématiquement soit physiquement avec ce dernier en stockage soit à la fabrication ou livraison. En d’autres termes, lors de la consommation d’un produit, le kanban qui lui était associé devient une carte de signalisation pour déclencher la production ou la livraison de pièces ou de produits en fonction de la demande client. Cette approche introduit donc la notion de droit à produire qui permet ainsi de faciliter la gestion d’un stock produit et la communication entre deux postes de travail, de deux îlots, ou de deux ateliers.
L’objectif de Taiichi Ōno était donc de produire ou de livrer au plus juste par rapport à la demande des clients. C’est un pilotage de la production s’inscrivant dans la philosophie du Juste à Temps. Le besoin client exprimé par une consommation se transforme de façon visuel (un kanban) en un bon à produire ou déplacer à poste afin d’arriver à une production sans gaspillage. En effet, en accord avec la démarche qualifié Lean, cela permet d’éviter la surproduction et de diminuer les délais.
Le système Kanban est donc un système d’information qui permet de faire remonter les besoins nécessaires vers les différents postes de travail situés en amont. Nous avons donc ici un système en flux tirés qui limite la production localement aux besoins exacts avec une gestion du stock au plus juste. Historiquement cette méthode révolutionnaire se démarquera des méthodes plus traditionnelles avec planification détaillée et ordonnancement à poste issus d’un calcul des besoins.
2. Kanban d’emplacement
Le Kanban d’emplacement, quant à lui, utilise des emplacements physiques désignés pour stocker les pièces ou les produits. De la même façon, cette déclinaison du kanban gère un équilibre entre la production d’un poste en amont et les besoins de celui qu’il fournit. Les étiquettes sont ici remplacées par des emplacements accueillant containers, palettes ou autre caisses produit. Chaque emplacement est associé à une quantité maximale de stock autorisée. Lorsque le stock atteint un niveau bas et qu’un emplacement se libère, le fournisseur situé en amont se doit de produire ou de livrer pour recompléter. A l’inverse, si tous les emplacements sont pleins, il n’y pas le droit de produire pour le poste fournisseur.
La différence fondamentale entre ces deux systèmes réside dans l’affiliation à un produit. En effet, le kanban d’emplacement se libère de cette notion, un emplacement acceptant ainsi tous types de produits. De ce fait, pour le kanban d’emplacement la référence à fabriquée n’est pas signifiée par une étiquette désignant un besoin particulier. Ce besoin est généré dans la plupart des cas par un ordre de fabrication issu d’un calcul de besoin MRP.
Nous avons donc ici aussi un système en flux tirés qui limite la production en contenant le stock en aval de chaque poste. C’est un système très visuel, que l’on soit fournisseur ou client, il suffit de jeter un œil au niveau des emplacements pour manager le flux. De plus, le risque de perte des étiquettes lors de la manipulation de ces dernières n’existe plus.
3. Bilan
Ainsi, la principale différence entre le Kanban classique et le Kanban d’emplacement est que le premier utilise des cartes de signalisation pré-affectées à chaque référence pour déclencher la production ou la livraison. Tandis que le second utilise des emplacements physiques pour stocker et récupérer les produits, indépendamment de la référence à fabriquer.
Mathieu Douteau Ingénieur consultant chez Wipsim
Mathieu est un ancien responsable de production. En 2021, Il s’est spécialisé dans la gestion des flux et la maitrise des en-cours. Depuis qu’il a rejoint Wipsim, il accompagne ses clients dans l’analyse de vos flux et dans la mise en œuvre des outils de pilotage de production.
Vous souhaitez en apprendre plus sur les solutions WIPSIM ?
Contactez nos experts pour plus d’informations ou une démonstration